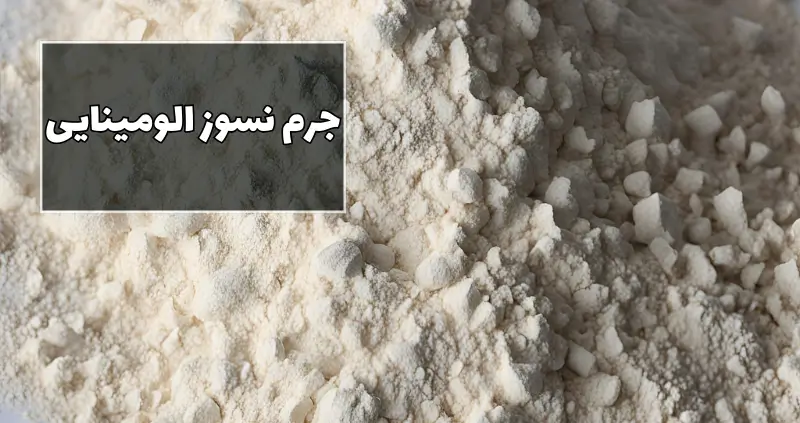
In today’s fast-paced and challenging world of industry, advanced materials are critical to ensuring the safety, efficiency and sustainability of processes and equipment. One of these key materials is alumina refractory mass, which, with its unique characteristics, plays a central role in protecting industrial systems against harsh and demanding conditions. Composed of an engineered aluminum and oxygen blend, this ultra-resistant material is capable of withstanding extremely high temperatures and corrosive chemical environments.
With the ever-increasing expansion of heavy industries and the growing demand to increase productivity and efficiency, alumina refractory mass has become one of the main pillars in the design and construction of industrial equipment and structures. From metal smelting furnaces to chemical reactors and jet engines, this material is ubiquitous and plays a vital role in maintaining safe and stable operation. However, today’s changing world brings new challenges and opportunities to improve and enhance this valuable material.
Chemical composition and structure of alumina refractory mass
Alumina refractory mass is basically an oxide ceramic mainly composed of aluminum and oxygen. Its main chemical composition is Al2O3 (aluminum oxide), which makes up about 90 to 99% of the total composition. Other chemical components are usually present as impurities or complementary additives, such as SiO2 (silica), Fe2O3 (iron oxide), and alkalis such as Na2O and K2O. These secondary compounds can affect the properties and behavior of alumina refractory mass.
Structurally, alumina refractory mass has a very rigid and dense crystal network, which gives it significant physical and chemical properties. Its crystal structure consists of aluminum and oxygen ions arranged hexagonally or rhombohedrally. This regular atomic arrangement is responsible for its high resistance to heat, corrosion and pressure. In addition, alumina refractory mass can exist in several different crystalline phases, including alpha, gamma, and delta, each of which has unique properties.
One of the important features of alumina refractory mass is its porous structure, which can be adjusted by controlling the production process. Porosity in this material can help increase resistance to thermal shock and prevent cracking. Also, the porous structure of alumina refractory mass allows the penetration and circulation of gases and liquids, which is useful for applications such as filtration and catalysts. Therefore, the precise control of the chemical composition and crystal structure is the key to achieving the unique properties of this valuable material.
Alumina refractory mass production process
The first step in the production of alumina refractory mass is the provision of suitable raw materials. The main sources of aluminum for this process include bauxite (the main ore of aluminum), metallurgical alumina (a byproduct of aluminum production), and calcined alumina (the result of heating bauxite). In addition, other additives may be added to the mixture to adjust the final properties and improve performance, such as oxides of silicon, iron, calcium and magnesium.
After preparing raw materials, there are different processes to produce alumina refractory mass. One of the most common methods is the smelting process, where raw materials are melted in high-temperature furnaces (around 2000°C). The resulting product can then be produced as a liquid cast or as solid molds. Another method is agglomeration, in which alumina powders are compacted and bonded together by heat and pressure. This method is suitable for producing more complex parts.
After initial production, alumina refractory mass may go through other post-processing steps. These steps include final firing at high temperatures (ceramic work), hot pressing to increase density and strength, and chipping operations such as grinding to reach the desired final dimensions and shape. Finally, strict quality control through standard tests such as compressive strength test, chemical corrosion test and microscopic examination is necessary to ensure the optimal performance of alumina refractory mass. A complex but precise manufacturing process is the key to guaranteeing the quality of this vital material in industrial applications.
Know more: Refractory cement and concrete
Applications of alumina refractory mass
One of the most important applications of alumina refractory mass is in steel and metallurgy industries. In these industries, alumina refractory mass is used as the inner lining of metal melting furnaces, the bed of furnaces, as well as parts and accessories. This material has the ability to withstand very high temperatures of melting metals (sometimes up to 1800 degrees Celsius) and protects against damage caused by oxidizing and corrosive environments. Without alumina refractory mass, the production of steel and other metals would be very difficult and expensive.
In ceramic and glass industries, alumina refractory mass also plays an important role. In ceramics and glass firing furnaces, this material is used for inner lining of furnaces, carrier platforms and other parts exposed to high heat. In addition to heat resistance, alumina refractory mass is also resistant to corrosive chemicals such as sodium, potassium and silicates that are present in glass making processes. These features increase the life and efficiency of the equipment.
Another application of alumina refractory mass is in chemical and petrochemical industries. In these industries, chemical reactions are carried out at high temperatures and exposed to corrosive substances. Alumina refractories are used to coat the inside of reactors, pipes, and other chemical processing equipment to protect them from corrosion and thermal damage. In internal combustion engines and gas turbines, internal parts are made of aluminum refractory mass to withstand very high combustion temperatures. These wide applications show the importance of alumina refractory in today’s industry.