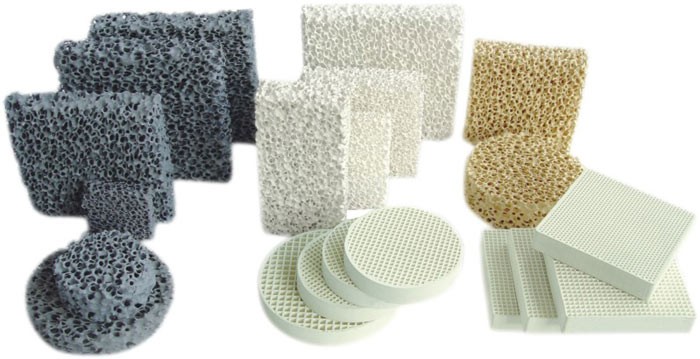
In today’s world of industry and technology, ceramic filter plays a vital role. These filters appear as a stable shield against filtration challenges and display unique capabilities. From water and wastewater treatment to gas separation and chemical and food filtration, ceramic filters have always provided a reliable solution. In this article, we will explain the types, applications, advantages and challenges of this advanced technology and introduce you to the subtleties and intricacies of making and using ceramic filters.
Types of ceramic filters
Ceramic filters include a wide range of types due to their diverse structure and unique features. One of the most important of these types is porous ceramic filters. This category of filters consists of ceramics full of pores and tiny holes, which gives them the ability to separate suspended particles and impurities in fluids.
Besides porous filters, microporous ceramic filters also have wide applications. Due to the finer and more precise structure of their pores, these filters are able to separate much smaller particles and are used in processes that require precise filtration. Also, nanopore ceramic filters with the ability to separate particles in nanometer sizes have shown very high efficiency in different fields.
Another type of ceramic filters are needle filters. Due to their special shape and structure, these filters are able to create high flow rates and effective performance in industrial processes. In fact, the use of these filters in many industries, including chemical, pharmaceutical and water and wastewater treatment, has created a significant improvement in the efficiency of the processes.
Applications of ceramic filters
Ceramic filters have been used in various fields due to their unique features, including corrosion resistance, cleaning and sterilization capabilities, as well as long service life. One of the most important applications of these filters is water and wastewater treatment. Ceramic filters, with the ability to remove suspended particles and pollutants in water, play a key role in providing safe drinking water and purifying industrial and agricultural water.
In addition, ceramic filters are also widely used in gas separation processes. These filters are used in industries such as petrochemical, steel and refineries with the ability to separate and purify different gases. Ceramic filters are also used in various sectors of chemical, pharmaceutical and food production to separate and purify materials.
Another important application of ceramic filters is in space and air fields. Due to their high resistance to harsh environmental conditions, these filters are used in air conditioning systems of airplanes and spaceships. Also, they have special applications in the defense industry, which are rarely discussed due to confidentiality.
Advantages of using a ceramic filter
Due to their unique characteristics, ceramic filters have many advantages compared to other types of filters. One of the most important advantages is their high resistance to corrosion. The ceramics used in making these filters tolerate chemicals and corrosive environments well and have high durability and useful life.
In addition, ceramic filters allow for easier cleaning and sterilization due to their porous and stable structure. This feature is very important, especially in sensitive applications such as drinking water treatment and pharmaceuticals. Also, the high life span of ceramic filters compared to other types, leads to significant savings in their maintenance and replacement costs.
Another important advantage of ceramic filters is their high efficiency in filtration processes. The special structure of these filters enables the separation of very fine particles and, as a result, significantly increases the quality of the final product. This feature is very important, especially in the pharmaceutical, chemical and food industries.
The technology of making ceramic filters
Ceramic filters are manufactured using advanced production methods. One of the most important of these methods is the use of porosity techniques. In this method, ceramic particles are placed in the form of lumps or powder in different molds and then by applying processes such as extruding, pressing and thermal processes, a porous structure is created in the ceramic. These methods lead to the production of porous ceramics with suitable pore cross-sections for filtration applications.
Also, in order to increase the efficiency of the ceramic filter, surface coating processes are also used. In these methods, by applying nano or micrometer layers on the ceramic surface, features such as increased erosion resistance, increased pressure discharge power and improved filtration capabilities are added to the ceramic filter. The use of these technologies in the manufacture of ceramic filters improves their performance and increases their applications in various industries.
Along with these production methods, continuous improvement in the design and shaping of ceramic filters is also important. Using different geometries, including needle, cubic and cylindrical filters, plays an effective role in optimizing fluid flows and increasing filtration efficiency. Also, the use of modeling and computer simulation techniques in the design of these filters, in order to improve performance and reduce manufacturing costs, has been considered.
Know more:
final word
Ceramic filters, as one of the most advanced and efficient filtration solutions in various industries, play a vital and irreplaceable role. From water and wastewater treatment to gas separation and clarification of chemical and pharmaceutical products, these filters, with their unique features, have always met the ever-increasing needs of industry and technology. Resistance to harsh conditions, ability to clean and sterilize, long life and great efficiency in filtration processes are some of the advantages that have made ceramic filters an indispensable tool in various industries. With continuous progress in the manufacturing and design technology of these filters and the expansion of their applications in the near future, we will witness significant developments in various industrial fields.